Given their requirement for heavy duty applications, the steel wires and cables are designed specifically for a large variety of operations. Not just that, the engineers ensure that the final product resists any kind of abrasion, wear and tear, and essential features for several applications, which include automotive, aerospace, instrumentation, recreation, medicine, appliances, and more.
In all of these, the durability and longevity are considered of primary importance for the buyers. Evidently, if the construction of a stainless steel wire is fudged, automatically the overall performance gets hampered. Some factors are crucial for determining the long life of those cables and wires. Let us learn more about them.
1. Lubrication for improving life period. Manufacturers apply specialized lubricant for increasing the life of a cable or wire. It helps improving fatigue life.
2. Plastic coatings as a perfect sealant. Generally, manufacturers prefer plastic coating to seal the lubricant and prevent dirt, moisture, and grit from affecting the cable.
3. Strength testing using workload. A reliable company follows a strict strength testing procedure using different workloads.
4. Testing the safety. Considering the costs and associated dangers, a safety testing is carried out on the stainless steel wires and cables.
5. Cutting and applications. Both flexible and non-flexible options are available in cables and wires. Precisely, the choice of cables and wires would depend upon their percentage of flexibility and suitability towards a particular application. Finally, it offers a brief insight into the performance and longevity of the products.
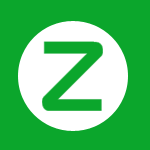